Amid the widespread changes of the last few years, organizations have a higher-level of understanding of the value process and performance management disciplines provide. Particularly the ability to create clarity around how work gets accomplished, fix broken processes, engage people in change, and stay flexible enough to support a range of priorities.
Consequently, process professionals are tapped to support a growing array of projects. To gain further clarity of how the role of BPM teams have shifted, APQC asked the respondents of its annual priorities and challenges survey, which organizational activities their process teams support.
Ways Process Supports the Business
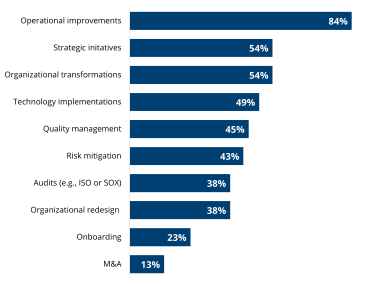
In this blog, we will discuss the primary way process teams support their organizations: operational improvements.
OPERATIONAL IMPROVEMENTS
Operational improvements are the proverbial bread and butter of process teams. Most teams continue to support traditional projects that focus on improvements in productivity, scaling the business, and cost savings. However, operational improvements are not a one and done endeavor.
Instead, they require an ongoing systematic approach to develop, monitor, and optimize the health of the organization’s operational processes.
- Developing Processes—includes understanding the current state of the organization’s processes and designing processes that are fit for purpose.
- Monitoring Processes—using control points and process-related KPIs to track the performance of processes. The goal here is to understand how the process is performing and identify improvement opportunities.
- Optimizing Processes—using improvement tools and methodologies to drill into the root cause of performance anomalies, identify the best fit solution (e.g., process redesign, developing business rules of process-related knowledge, reallocation of roles, or technology application), and work with the business to implement the solution.
There are several variations on how process teams tackle operational improvements. However, they all include a core process toolkit and active partnership with the business.
For example, CMI uses a continuous improvement team comprised of centralized resources and decentralized process champions to standardize processes, identify opportunities, and execute projects throughout its Shared Services. The team combines a mix of process mapping, benchmarking, and Lean Six Sigma methodologies in its project execution.
While Pacific Northwest National Laboratory’s process team developed a database of standardized processes, procedures, and guidelines for employees. This standardization served the organization well during the onset of the pandemic. The combination of standardized processes and collaboration tools meant the research institutes didn’t need build everything from scratch, just simply scale.
For more information on this topic check out: Operational Improvements: Process Supporting the Business.
This blog is the beginning of an ongoing series exploring the myriad of ways process teams support their organizations. You can expect a deeper dive on each way throughout the year. This series will include videos, podcasts, blog posts, and articles. So please stay tuned.
For more process and performance management research and insights, follow me on Twitter at @hlykehogland or connect with me on LinkedIn.